Our Process: Natural Dyes
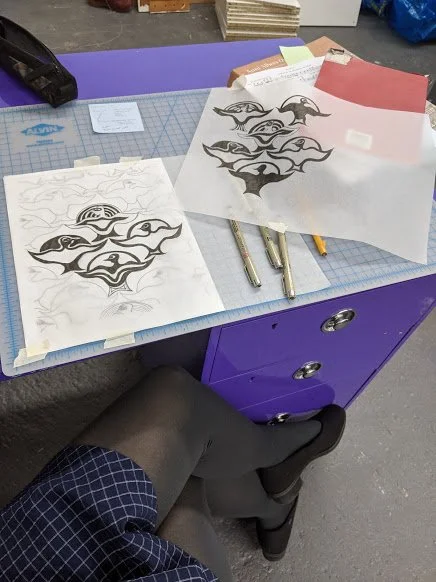

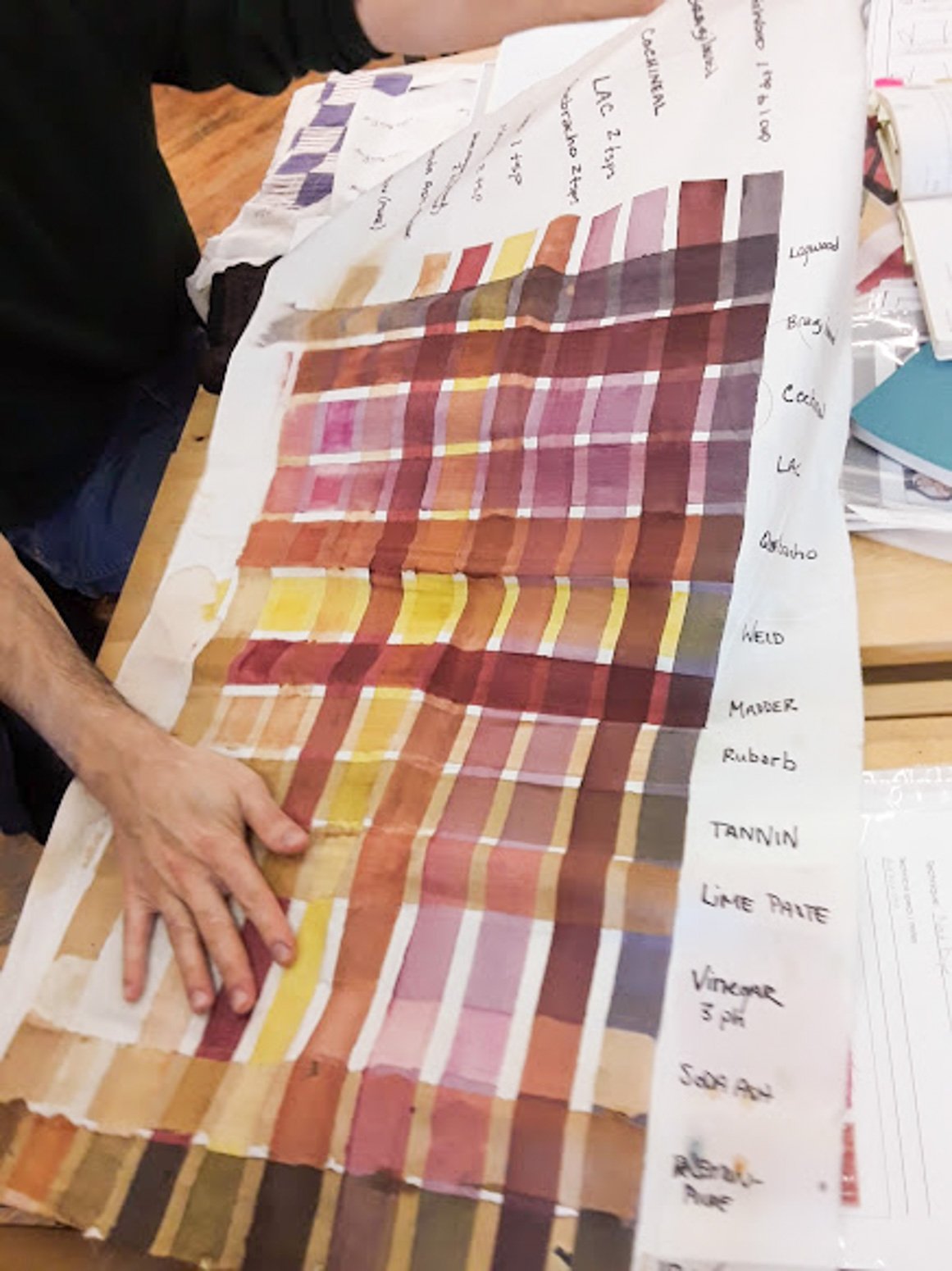
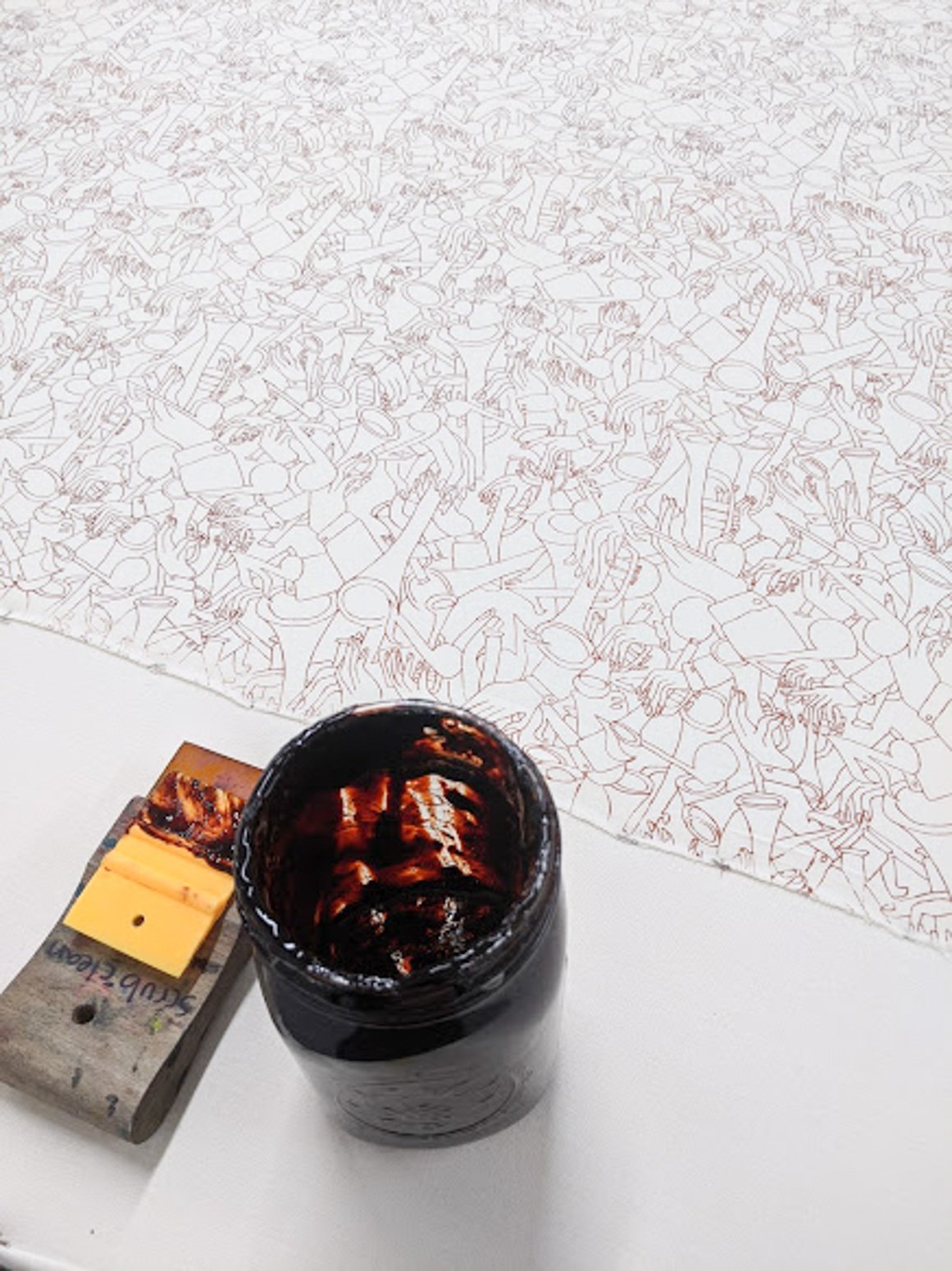
1. Scour
Before we scour, we must thoroughly wash the fabric to remove extraneous substances: sericin in the case of wild silk, and gums in cotton and oil in wool, that would prevent the dye from being imbibed evenly. This is done in a big pot brought to a boil with a gentle detergent like synthrapol and some washing soda. Cotton must be boiled for at least an hour, silk and wool being sensitive to temperature changes, must be simmered but not boiled.
2. Mordant
A mordant—from the French “mordre," to bite—is a mineral (sometimes derived from plants, like the symplocos plant in Indonesia) that allows the dye to chemically bond with the fiber. Without a mordant, the dye will bleed out at the first wash, and a mordant improperly applied will result in splotches and unevenness on the finished fabric. This again, we do in a big pot, on the stove or on the fire. There area variety of mordants but the one that has been used since Roman times, and the one that we still use at Setton, J. Textiles, is aluminum sulfate, often shortened to alum.
3. Print
All our patterns start life with pen and paper. Once the design is finalized and the repeat set up, we make the screens. Each color requires a different screen. This is the“dirtiest” part of our process since it uses a photographic type emulsion to burn the image onto the mesh of the screen. The inks, a decoction of dyestuffs from plants or animals thickened with guar gum, are mixed the night before printing to allow the color to develop, and the consistency to settle. We stretch and pin the fabric in eight-yard segments on our printing table, and print in alternate panels, allowing the ink to dry so that it won’t smudge before returning to print the open space.
4. Cure and steam
The fabric is set aside to rest for at least two weeks to let the dye penetrate; after which the fabric is steamed, to fix the dye; and rinsed, to remove the excess thickener and color.
5. Cut and Sew
We make our garments in the Garment District of Manhattan or with a lovely seamstress in Willimantic, CT. We print in small runs, the process is lengthy, and each batch is different; so if you see something you like, buy it now, because when it’s gone its gone.